When a Robot Designs Its Own Experiments
MIT’s Intelligent Towing Tank Automates Data Collection
Dixia Fan, an assistant professor at Westlake University in China, calls his former lab at MIT the “Lab of Pink Coach.” In a peek at the MIT Smart Hydrodynamics Lab over Zoom, he points to a secondhand pink couch—a suitable place to sit and watch his robot run experiments over and over in a water tank called a towing tank. “So, I’m a coach sitting on a couch, training the next Michael Jordan of the towing tank,” he says. “I personally cannot dunk, nor can one person do that many experiments. But this guy can do it.”
“If we can put another brain into these machines, they will not just repeat experiments, but design them.”
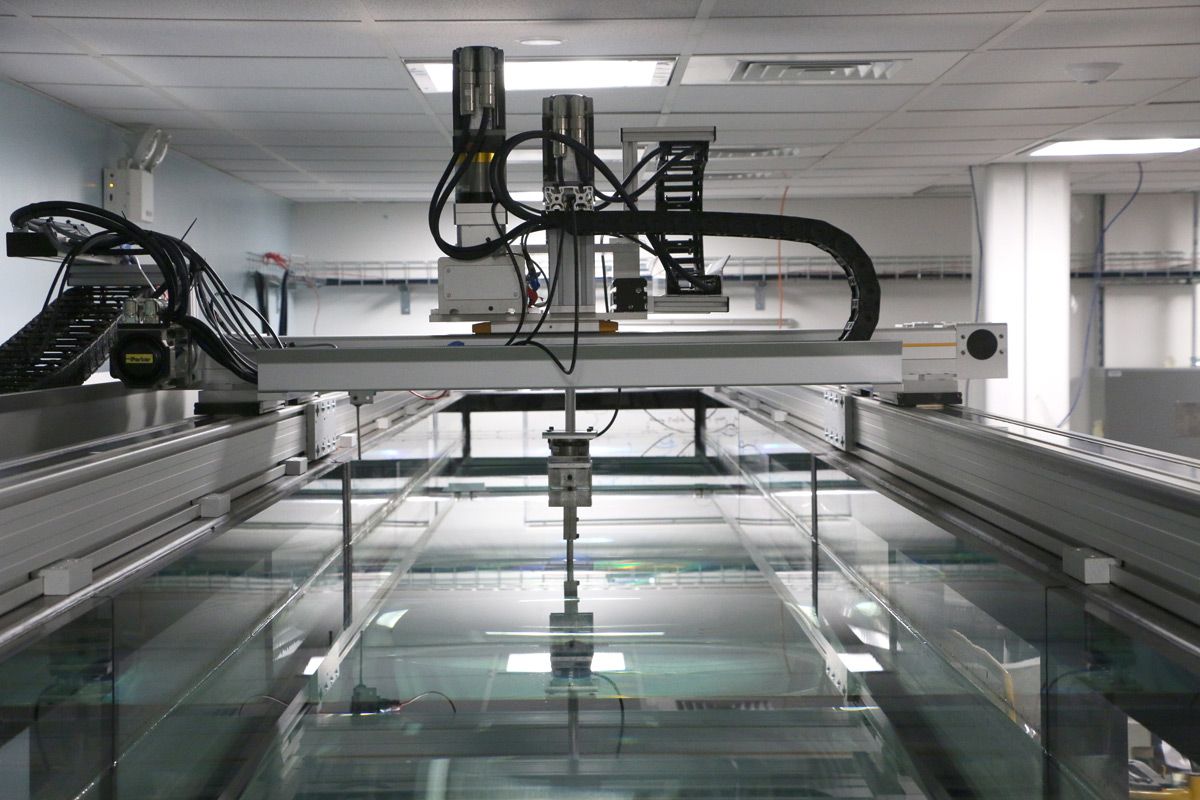
The Intelligent Towing Tank. (Image credit: Dixia Fan)
The “Intelligent Towing Tank” (ITT) is about 9 meters long, 0.9 meters tall, and 0.9 meters wide (30 x 3 x 3 feet). The robot looks nothing like Michael Jordan, or Michael Phelps for that matter. It’s a boxy apparatus that sits on two rails atop the tank that run its full length. As it moves, it tows an object of a scientist’s choosing in the water below.
Along the way, it collects data on hydrodynamics—measuring, for instance, how much resistance the object encounters. The robot changes certain parameters, such as speed and angle, and runs the experiment again. It collects data automatically, doing laps day and night, running a Ph.D.’s worth of experiments in just two weeks.
And that’s without its intelligent selection of which experiment to run next, which speed and angle to use on the next lap. If you want to manipulate eight parameters, you pick 10 settings for each parameter. That would require 108—a hundred million—experiments to map out the space of possibilities, every combination of speed, angle, and so on. Researchers call the exploding number of possibilities the “curse of dimensionality.”
The ITT takes a shortcut. It does a few random experiments, which it extrapolates to other settings. Then it calculates the region in the parameter space it’s most uncertain about. It runs an experiment with those parameters inside this region. It repeats this process until it’s sufficiently certain about most of the space. Instead of running a hundred million experiments, the ITT needs only a few thousand.
Fan notes that other labs use robots to automate data collection. Drug companies, for instance, employ them to test the properties of vast numbers of molecules. “Lab automation is very advanced,” he says. “But if we can put another brain”—in addition to the human scientist’s—“into these machines, they will not just repeat experiments, but design them.”
Pipe Dream
Much of the ITT’s experiments have involved marine-drilling risers, which are pipes connecting oil wells on the seafloor to platforms floating on the surface. Towing a scale model of a riser through the tank simulates the movement of ocean currents past a stationary riser, which create vortices around it, the way river water creates whirlpools behind rocks and logs in rapids. These vortices cause the pipe to vibrate. Oil companies want to reduce those vortex-induced vibrations, which can cause pipe fatigue and increase the likelihood of oil leakage.
In the real world, a riser often extends hundreds of meters (thousands of feet), consisting of many pipes about 0.3 meters (1 foot) thick. Although each section is rigid, the entire span is flexible. As water flows around it, Fan says, “the whole thing vibrates.” Engineers would like to create computational models and predict the riser’s movement, but the problem is too difficult. Instead, they collect hard data on physical models of a section and put those numbers into a mathematical model, simplifying the computations.
In Fan’s studies of risers, the ITT tows a vertical pipe about 46 centimeters long and 4 centimeters thick (18 x 1.5 inches). The robot atop the tank has sensors, called load cells, to measure outputs, including drag (resistance). It also controls input parameters such as the frequencies, directions, and amplitudes of vibrations. Not everything is automated; researchers pick relevant parameters and the ranges of values worth exploring.
The ITT selects input parameters for the next experiment in order to minimize uncertainty. There are two kinds of uncertainty it deals with. First, there’s measurement uncertainty. If you run an identical experiment twice—two trips down the tank using the same parameters—you might get different results because of imprecision in the sensors or the sheer variability of nature, especially when dealing with the chaos of vortices. The second type is model uncertainty, or imprecision in predicting the measurement for a given experiment. Combined, the two uncertainties produce total uncertainty. The ITT collects data until total uncertainty falls below a given threshold.
Instead of trying 100 million different combinations of parameter values, the system reached certainty in its predictions after fewer than 4,000 tests.
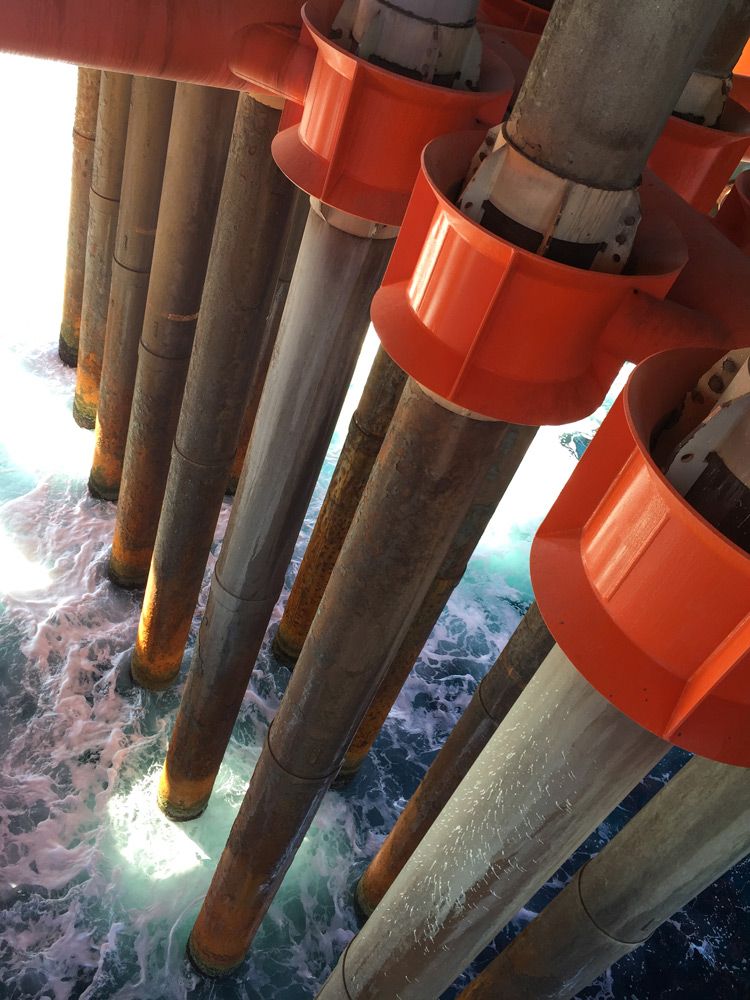
Vortices created by an ocean current moving around oil risers.
To decide on the threshold, Fan first calculates measurement uncertainty. He runs thousands of experiments and examines variance in the data. Quantifying measurement uncertainty is not an exact science. “Basically, you need to know your machine,” Fan says. “I started getting a feeling of what this error bound is. Here is where the research experience comes in.”
Fan doesn’t expect total uncertainty to match the measurement uncertainty—model uncertainty exists in our understanding of any real-life systems. Instead, he allows some leeway. When the ITT’s uncertainty about the haziest regions of the parameter space drops below measurement uncertainty times three—an educated guess and safety factor chosen by Fan—it has reached the threshold and its job is complete.
In one study, published in Science Robotics, the team explored a space defined by eight parameters, training a model to predict a value called the “lift coefficient in phase with velocity.” Instead of trying 100 million different combinations of parameter values, the system reached certainty in its predictions after fewer than 4,000 tests.
It’s assumed that the model is not only certain, but also somewhat accurate. In future work, Fan will also make sure the models become both certain and correct.
Tower of Babel
The robot’s software uses several languages. Power PMAC controls its motion. Software written in C# and LabVIEW™ reads data from the sensors. And “MATLAB serves as the brain for the system,” Fan says, tying the pieces together. Instead of rewriting all the code in one language, he coordinates the other pieces through a MATLAB® script. MATLAB also calculates uncertainty and decides which experiment to run next.
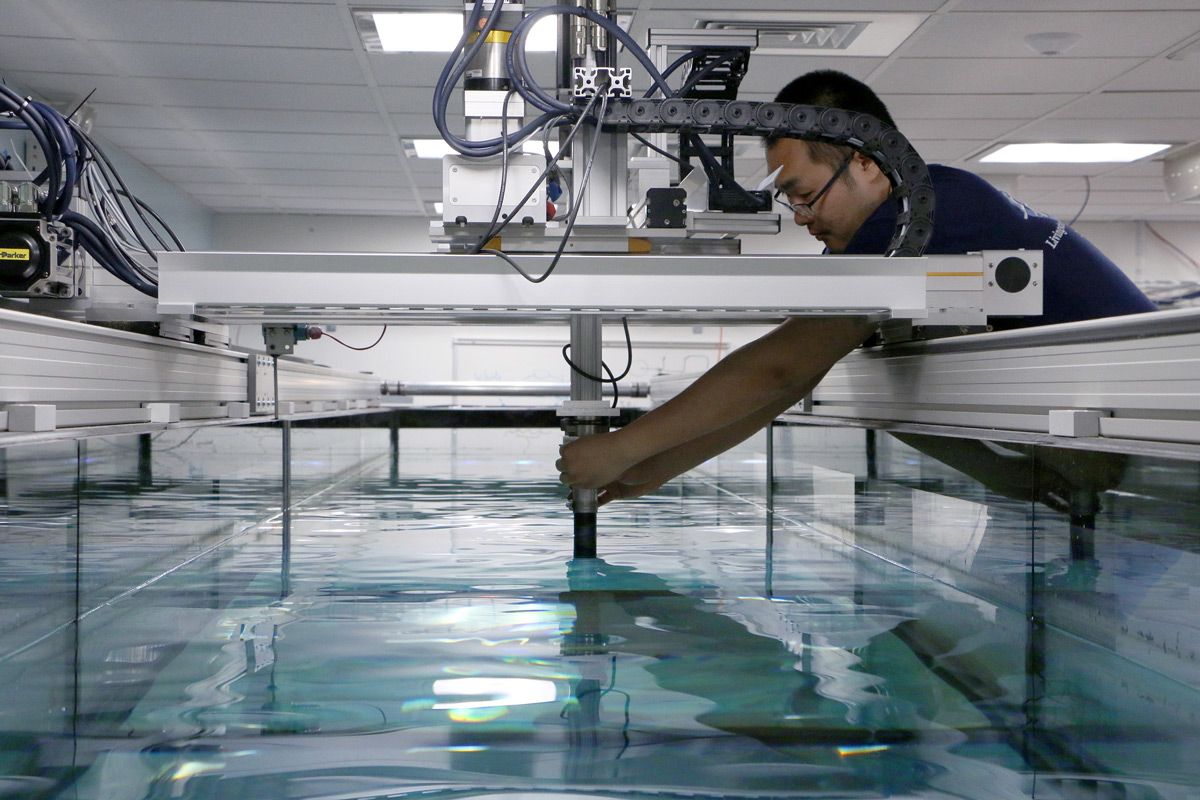
Dr. Fan adjusting the Intelligent Towing Tank. (Image credit: Dixia Fan)
MATLAB enables the ITT to coordinate subsystems written in several languages, calculates uncertainty, and decides which experiment to run next.
To pick experiments, the system employs a mathematical technique called Gaussian process regression (GPR). Imagine a space defined by only two parameters (maybe velocity and angle). The space can be viewed as a landscape, where the input parameters define latitude and longitude. For each spot on the landscape, the system has a level of uncertainty in predicting the output (such as drag). This uncertainty can be pictured as the altitude at that latitude and longitude. Some areas will have hills, where it’s hard to know ahead of time what the drag will be for that velocity and angle. GPR defines that landscape by building those hills. Once a measurement is taken at a location—preferably where a tall hill sits—GPR flattens that hill. MATLAB has a package called Fit GPR in Optimization Toolbox™ that builds these landscapes, in any number of dimensions. “We are trying to make friends with uncertainty,” Fan says. “Let’s use uncertainty as a guide.” The system selects the next experiment by finding the tallest hill.
Fan says that instead of GPR, he could use neural networks to predict measurements, but GPR offers a more natural way to quantify uncertainty. There’s no consensus on how to do so with neural networks.
Fan appreciates that MATLAB packages helped him through every stage of his project. Fan is a hydrodynamics expert, but not a software expert. In the early stage, he used Reinforcement Learning Toolbox™ to quickly prototype and validate his ITT system. When he was ready to further improve the performance of the ITT, he customized the MATLAB toolboxes. Instead of using inflexible software packages, or rewriting thousands of lines of code by hand, he can look inside MATLAB toolboxes, read the comments, understand the code, and adjust a few lines as needed.
Swimming Lessons
Mapping parameters such as vibration frequency to drag could help oil companies design safer and more efficient risers. Then they could optimize pipe thickness, or the location of devices that reduce vibration, finding designs that reduce drag (and the chance of disaster). The design models could also act as “digital twins” of specific real risers, modified to age or incorporate repairs as the real risers do.
“This experimental method—or even experiment methodology or philosophy—is not restricted to fluid mechanics.”
The work offers lessons beyond the water tank. “This experimental method—or even experiment methodology or philosophy—is not restricted to fluid mechanics,” Fan says.
It could also apply to structural mechanics. An intelligent 3D printer might build a material or structure, then test its strength or other properties, and use that information to print something new. Or in the life sciences, a robochemist might create a drug, test its efficacy in a flask, and design another new drug. In the meantime, robots will still be in training before designing their own slam dunks.
Read Other Stories
ROBOTICS
Exploring the World’s Largest Ecosystem — 500 Meters Below the Ocean Surface
Nat Geo Develops Underwater Robotic Camera to Explore the Deep
ROBOTICS / AUTONOMOUS SYSTEMS
Trusting Robots to Navigate New Spaces
New Algorithm Boosts Robustness of Robot Perception